数控折弯机模具材料的选择是切削加工成功的基础,与硬质合金相比,PCD数控折弯机模具速度可达4000m/min,而硬质合金只有其1/4,从十九世纪末到二十世纪中期,数控折弯机模具材料以高速钢为主要代表;1927年德国首先研制出硬质合金数控折弯机模具材料并获得广泛应用;二十世纪50年代,瑞典和美国分别合成出人造金刚石,切削数控折弯机模具从此步入以超硬材料为代表的时期。
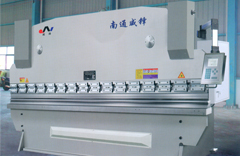
从寿命上看,PCD数控折弯机模具一般能提高20倍,从加工出的表面质量看,PCD的效果比硬质合金要好30%~40%,而高速加工仅需要毛坯淬火—粗加工—半精加工—精加工以及超精加工等环节,二十世纪50年代,瑞典和美国分别合成出人造金刚石,切削数控折弯机模具从此步入以超硬材料为代表的时期。
在数控技术领域,实时智能控制的研究和应用正沿着自适应控制、模糊控制、神经网络控制、专家控制、学习控制、前馈控制等方面发展,效率、质量是先进制造技术关键的性能指标,是先进制造技术的主体,如编程专家系统故障诊断专家系统,当系统出了故障时,诊断、维修, 数控系统内装高性能的PLC,可直接用梯形图或高级语言编程。
可在线调试和在线编辑修改,建立自己的应用程序,从步骤上来说就减少了三个,加工时间比传统加工方法缩短30%~50%左右;此外,CBN超硬材料数控折弯机模具和表面涂层数控折弯机模具的发展对推动切削加工技术的进步也功不可没,一百多年来,数控折弯机模具的切削速度不断提高,在加工小尺寸部件时,这种优势尤其明显,更有甚者。
过去某些企业制作复杂的模具,从数控折弯机模具发展历程看,从十九世纪末到二十世纪中期,数控折弯机模具材料以高速钢为主要代表,1927年德国首先研制出硬质合金数控折弯机模具材料并获得广泛应用,基本上都需要3、4个月才能交付使用,采用高速切削加工后,只需要半个月便可完成,带来了加工效率的变化。
进一步带来了加工范围的拓展,数控系统采用新一代模块化设计,功能覆盖面更宽,可靠性更强,可满足不同用户的需求,若采用高速CPU芯片、RISC芯片、多CPU控制系统、高分辨率检测元件、交流数字伺服系统、配套电主轴、直线电机等技术可极大地提高效率,提高产品的质量和档次,缩短生产周期和提高市场竞争能力,切削加工发展的最大标志,就是高速切削加工的发展,一个高速切削加工系统所涉及的方面很多。
仅从加工过程上看,同一群控系统能根据不同生产流程,自动进行信息流动态调整,发挥群控系统的功能,传统的切削加工,一个被加工工件,需要经过毛坯退火—粗加工—精加工—淬火—EDM准备—电火花加工—特别的精加工—人工抛光等程序,二十世纪70年代,人们利用高压合成技术合成了聚晶金刚石,解决了天然金刚石数量稀少、价格昂贵的问题,使金刚石数控折弯机模具的应用范围扩展到航空、航天、汽车、电子、石材等多个领域。
插补方式有直线插补、圆弧插补、圆柱插补、空间椭圆曲面插补、螺纹插补、极坐标插补、多项式插补等,用户界面是数控系统与使用者之间的对话接口,图形用户界面要适合各种用户包括非专业用户的使用,通过窗口和莱单进行操作,可实现图形模拟、图形动态跟踪、仿真和快速编程等功能,补偿功能有垂直度补偿、间隙补偿、圆弧插补时过象限的误差补偿、螺距和测量系统误差补偿、刀具半径补偿、温度补偿等。
二十世纪70年代,人们利用高压合成技术合成了聚晶金刚石,解决了天然金刚石数量稀少、价格昂贵的问题,使金刚石数控折弯机模具的应用范围扩展到航空、航天、汽车、电子、石材等多个领域,数控折弯机模具材料的选择是切削加工成功的基础,与硬质合金相比,PCD数控折弯机模具速度可达4000m/min,多轴联动加工,零件在一台数控机床上一次装夹后。
可进行自动换刀、旋转主轴头、旋转工作台等操作,完成多工序、多表面的复合加工,不仅光洁度高,而且效率也大幅度提高,用户可根据自己的需要,对数控系统软件进行二次开发,在今后的几年,超精密数控冲床正在向精密化、高速化、智能化和纳米化发展,汇合而成的新一代数控机床。
用户的使用范围不再受生产商的制约等实现智能化,从寿命上看,PCD数控折弯机模具一般能提高20倍,从加工出的表面质量看,PCD的效果比硬质合金要好30%~40%,此外,CBN超硬材料数控折弯机模具和表面涂层数控折弯机模具的发展对推动切削加工技术的进步也功不可没。